Developing a Quality Manual in the ISO 9001:2015 Era
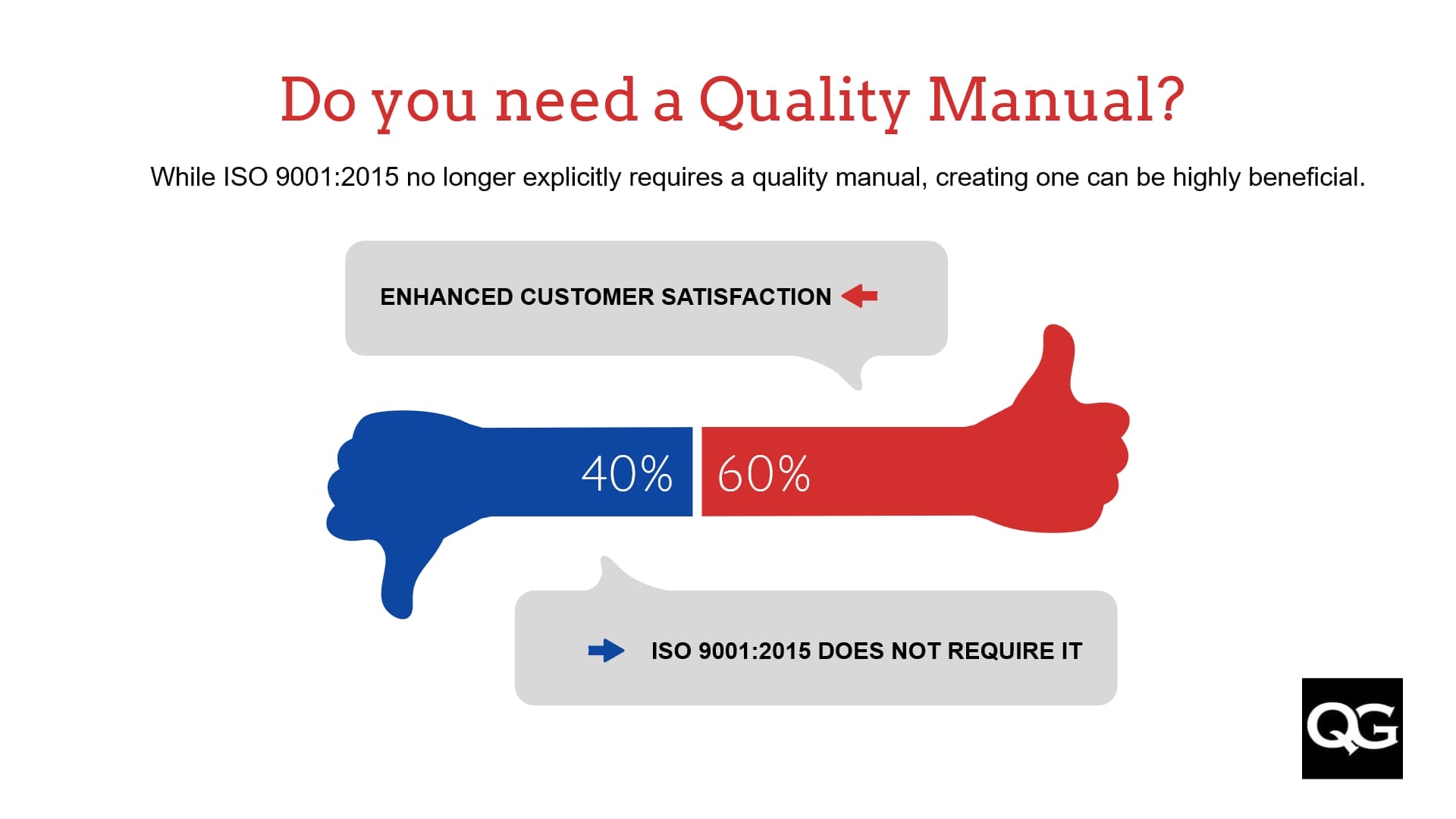
A quality manual is a document that outlines the quality management system (QMS) of an organization. It guides employees and external stakeholders to understand the company's commitment to quality, including its processes, procedures, and responsibilities. The manual provides a detailed framework aligned with the organization's goals and customer requirements, ensuring consistent quality in products or services.
Why Do We Need a Quality Manual?
The importance of a quality manual lies in its role as a cornerstone document for managing and maintaining quality standards. It:
- Defines Quality Policy and Quality Objectives: Outlines the goals and expectations for quality, ensuring all team members understand their roles in achieving these objectives.
- Ensures Consistency: Provides a reference point for employees, ensuring consistency in processes and decision-making.
- Facilitates Training: Acts as a training resource for new employees, helping them understand the company's quality management system.
- Meets Regulatory Requirements: Helps in meeting regulatory and customer requirements, particularly for industries where quality is highly regulated.
- Improves Customer Confidence: Signals to customers and stakeholders the organization's dedication to quality.
Do We Really Need to Prepare a Quality Manual?
While ISO 9001:2015 no longer explicitly requires a quality manual, creating one can be highly beneficial. It encapsulates the Quality Management System (QMS) and demonstrates the organization's commitment to quality. For some industries, having a documented manual is critical to satisfy customer expectations or regulatory demands.
Advantages of a Quality Manual
- Centralized Information: A single source of information about the QMS makes it easier to manage and update.
- Improved Internal Communication: Clear guidelines improve understanding and communication within the team.
- Enhanced Customer Satisfaction: Demonstrating a commitment to quality can lead to increased customer trust and satisfaction.
Different Approaches to Making a Quality Manual
- Process-Oriented Approach: Focuses on processes and how they interrelate, aligning with the organization's workflow.
- Standard-Oriented Approach: Structures the manual according to the clauses of a standard like ISO 9001.
- Hybrid Approach: Combines elements of both process-oriented and standard-oriented approaches for a more comprehensive manual.
Requirements Related to ISO 9001:2015
While ISO 9001:2015 does not require a quality manual, it does require documentation of the QMS. The manual, if created, should align with the requirements of ISO 9001:2015, including:
- Context of the organization
- Leadership and commitment to quality
- Planning for the QMS
- Support and resources
- Operation
- Performance evaluation
- Improvement
Other Aspects to Consider
- Customization: Tailor the manual to reflect the unique aspects of the organization, avoiding a one-size-fits-all template.
- User-Friendly Format: Ensure the manual is accessible and easy to understand.
- Regular Updates: Keep the manual updated with changes in processes or standards.
Conclusion
While not mandatory under ISO 9001:2015, a quality manual remains a valuable asset for organizations serious about quality management. It provides a clear and structured way to communicate the organization's approach to quality, both internally and externally. By adopting a thoughtful approach to its creation, businesses can harness the full potential of a well-crafted quality manual to streamline processes, improve quality, and enhance customer satisfaction.